Streamlining maintenance with IoT
Have you ever faced the uncertainty of whether you turned the faucet off completely? Now imagine you had a thousand faucets and some of them must be turned on and others turned off for everything to run smoothly. That is the situation with Stora Enso, except the faucets are hand valves, responsible for transporting liquids around the facility. Having to check every single one of those hand valves manually, the risk of error is present and might lead to a waste of fluids or safety risks. To prevent that, Stora Enso decided to bring IoT into the game.
Automatic monitoring instead of manual checks
Since paper and cardboard manufacturing uses liquids, there are a lot of pipelines and valves. During planned maintenance, flows must be stopped and, of course, the valves opened again before restarting production. Some valves are still hand-controlled and operating them is time-consuming in massive manufacturing plants. Leaving valves in the wrong position in production restarts might lead to additional downtime and safety risks.
Marko Yli-Pietilä, the Head of Smart Operations at Stora Enso is familiar with different IoT solutions. “Retrofitting position sensors to hand valves typically requires a lot of wiring, which is expensive when you have so many in your production ”, says Yli-Pietilä. “We want to monitor our hand valves digitally in a cost-efficient way. There was not a suitable wireless hand valve angles sensor commercially available so we needed a partner to co-develop one with us”, he continues. Haltian had already developed different kinds of wireless sensors and they were ready to be modified for the purpose.
It’s all about solving problems
Stora Enso has a certain mindset towards IoT and digital solutions. They don’t run IoT projects for the sake of IoT itself, but rather to solve problems they have discovered in their processes. “We don’t have an IoT development program, we see IoT as a technology that can be used to solve problems. IoT is not even a solution, but more like a tool for problem-solving”, Marko Yli-Pietilä explains. Practicality is the key. Yli-Pietilä’s advice is to not over-complicate things with cool gadgets but to keep it simple. Industries all over the world are streamlining their systems by reducing the number of individual add-ons, integrations, and software, and bringing it all together into a fully functional, easy-to-maintain ecosystem. Bear this in mind when you are planning your next digitalization project!
…IoT is not even a solution, but more like a tool for problem-solving
Marko Yli-Pietilä, Head of Smart Operations, Stora Enso
Should you pay more attention to what your competitors are doing or find your path then? “We do some benchmarking but we don’t copy our competitors, simply because they’re not us”, Yli-Pietilä states. “We are the experts in our environment and of our problems. We understand the problems better than anyone but solving them requires partners who are experts in their domain”, he continues.
Don’t waste your time – or money
Stora Enso has a great guideline for their IoT projects: the value must be greater than the investment. “If our only goal would be getting rid of the problem, that would be easy with current solutions. But solutions must be cost-efficient, and that rules interesting technologies out in many cases” claims Marko Yli-Pietilä.
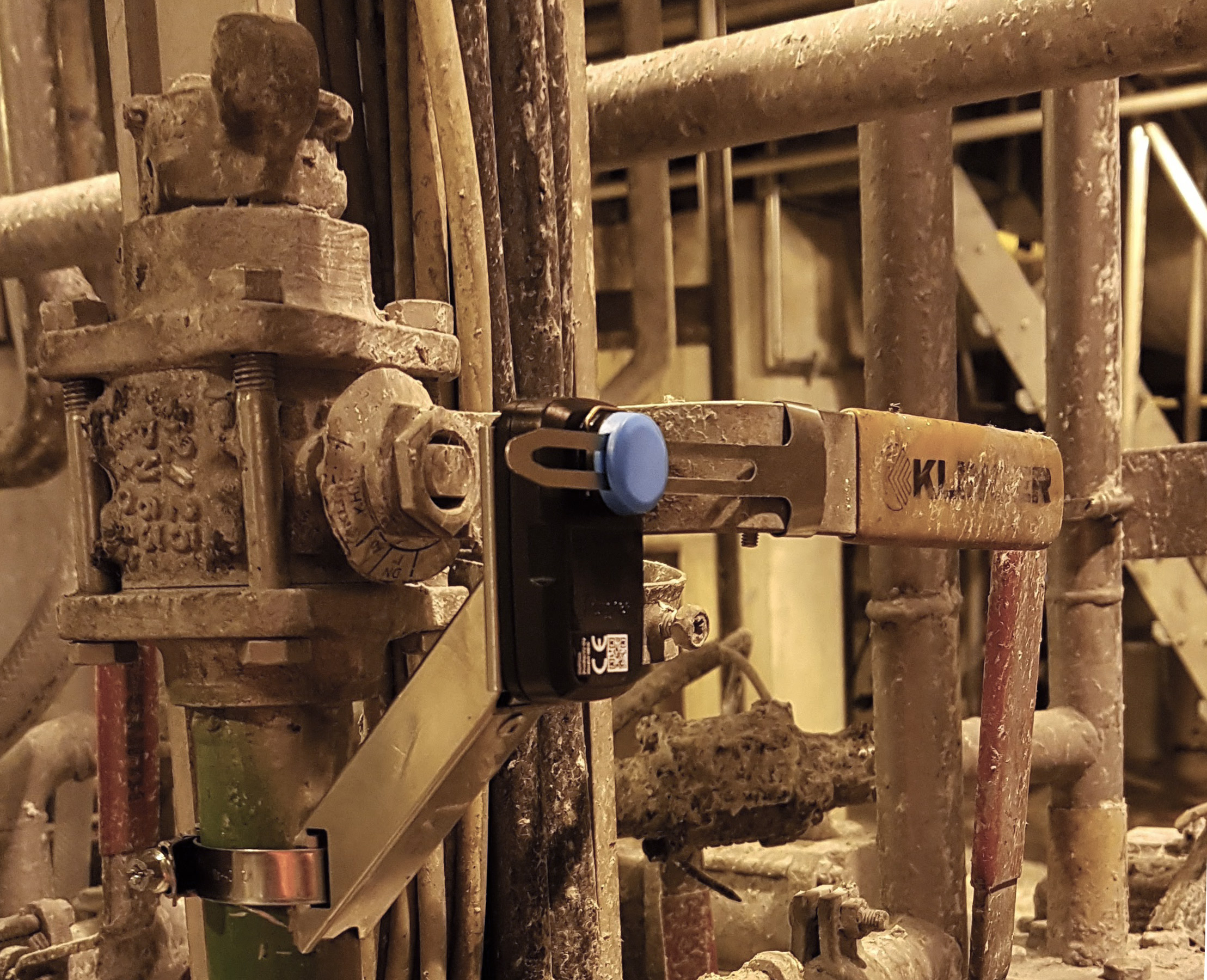
That’s a wrap!
It’s important to know your problems and goals before you start developing solutions. Then you need to have a clear concept before starting the hands-on work. It is followed by a proof-of-concept to test your MVP or minimum viable product. Running a suitable pilot before the final decision on implementation is the most cost-efficient way to lower risks of failure when you are scaling a solution out. The wireless IoT hand-valve position monitoring solution was developed in cooperation with Haltian using this iterative and agile approach.
“After the proof-of-concept phase was done we continued with the pilot to run the solution in actual use in one mill”, says Yli-Pietilä. “During the pilot, many problems not visible in the proof-of-concept emerged and were solved”, he continues. “After a certain period, we looked at the results and collected user feedback. After final modifications, a decision to use the solution in other mills was made.“
Read more
This article is a part of a series about starting with IoT solutions. Read the other articles here:
- Smarter buildings with IoT – Interview with Jari Tiirikainen from facility management company ISS
- Starting your first IoT project – Marcus Stenstrand, Fingrid
- What makes a building smart? – James McHale, Memoori