Reduce facility maintenance costs by 23% with data-driven cleaning
Facility maintenance, such as cleaning is labour-intensive business – it’s difficult to grow profitability. This case study explains how an international Facility Maintenance company, the Lindström Group reduced costs by increasing cleaners’ working efficiency by 23% by implementing data-driven cleaning with IoT sensors in their facilities.
Now cleaners receive a message whenever there is a toilet or washroom that needs cleaning, or hand towel replenishment – every cleaner saves two hours of working time daily by avoiding unnecessary walking!
In this article, you’ll learn about data-driven cleaning and how to calculate your savings with a Smart Washroom solution!
What are the challenges in today’s Facility Maintenance business?
Facility Maintenance service, such as cleaning of public spaces, is a labour-intensive business. It is also a substantial cost for airports, conference venues, shopping malls, hospitals and schools, and more.
Tidy washrooms with replenished hand towels and soap dispensers are crucial for business – they improve customer and visitor experience, and increase revenues at shopping malls, among many other benefits.
For Facility Maintenance service providers, cleaning is a rapidly growing business. However, it is not easy to increase profits in this labour-intensive service. Purchasing the cheapest paper towels and liners will not deliver sufficient cost reductions.
The biggest challenge for Facility Maintenance service providers in cleaning is: How to reduce costs by increasing cleaners’ working efficiency while maintaining an excellent service level?
The cleaning staff taking care of large commercial and public spaces such as airports must walk long distances during an average workday. They must frequently move from one washroom to another, to check whether the next toilet on the task list needs cleaning and if hand towel dispensers have enough tissue.
In addition, the dispensers, in the many restrooms of shopping malls, airports, and hospitals, serving thousands of customers and visitors daily, run out of towels frequently.
Without prior knowledge of which toilets really need cleaning, or where are the towel dispensers in need of replenishment, the cleaning staff typically walk through a scheduled and pre-programmed route. However, much of this walking is unnecessary.
According to Lindström Group, the leading multi-national B2B textile services provider based in Finland, cleaners can end up walking up to 10 kilometres per day when taking care of their duties in public facilities.
The solution is implementing data-driven cleaning with IoT sensors!
The Lindström Group decided to harness the latest technologies to implement data-driven cleaning and to increase cleaning work efficiency.
The company deployed Haltian’s wireless IoT sensors into thousands of washrooms located in public facilities.
In hand towel dispensers, small sensors with an ultra-sound distance meter measure the fill level of towel tissue and report over a wireless connection to The Lindström Group’s workforce management system if a dispenser needs replenishment.
Presence sensors count the number of visitors so that cleaners can focus on the most visited locations, and react quickly to washroom visitor pattern changes.
Now, The Lindström Group’s thousands of smart hand-towel dispensers notify cleaners automatically via their mobile Apps, which toilets require cleaning and hand towel replenishment to avoid spending time on unnecessary walking.
What are the benefits?
After taking the smart washroom solution into commercial production use, The Lindström Group has been able to reduce cleaners’ daily walking distance by 2.3 kilometres, a 23% reduction. As a result, 23% of the walking time could now be translated into cost savings, or used for other productive use!
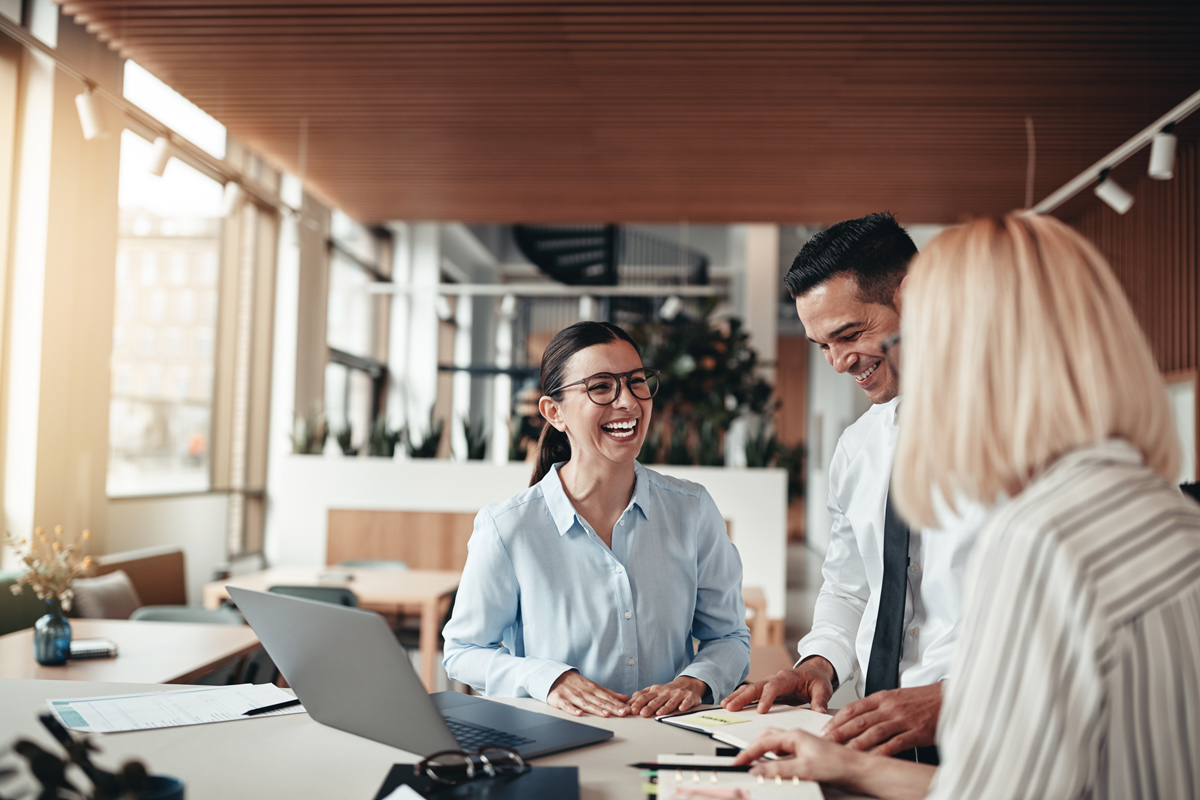
How to calculate this business case for a facility maintenance company?
Based on the Smart Washroom case study, it is easy to estimate a Business Case for any Facility Maintenance service provider.
A cleaner who is walking 10 kilometers per day would spend roughly two hours, i.e., 25% of a regular 8-hour workday on walking, when a nominal walking pace of 5km/h is assumed.
Imagine, if your Facility Maintenance company had a staff of 1,000 employees doing cleaning, in a total of 2,000 hours of daily working time would be spent on walking.
If an average salary of, say, €10 per hour is assumed, the daily cost of walking becomes €20,000. The total costs of walking time with a staff of 1,000 cleaners could then be as high as €5,200,000 annually.
Estimating cost savings
By applying the learnings from the Smart Washroom case study, i.e., a 23% reduction in walking, you can easily estimate the potential cost savings in your company.
If 23% of the total walking time is deemed unnecessary and could be reduced by a Smart Washroom solution, the associated costs of €5.2 million would be reduced by €1,200,000 annually!
Learn to optimise your workflow and reduce costs!
If you want to increase your Facility Maintenance efficiency and reduce costs through IoT sensors and smart IoT solutions, like data-driven cleaning, contact us!
Download the Lindström Group’s Smart Washroom case study here!